Products / Turnkey Powder Gypsum Plants
Our company has an experience on powder gypsum plants over 25 years. Along with the turnkey projects and plant subcomponents installed up to now, CMS is a solution partner for the leading long-established powder gypsum manufacturers in Turkey and in the world. Turnkey plants within the capacity range of 100t/day.-600t/day. are designed and manufactured including almost all subcomponents. Crushing units and automation works are designed and manufactured by our suppliers under strict controls.
Unlike traditional rotary kilns, patented CMS rotary kilns (AFD series) have horizontal (0º, no incline) orientation. Distinct kiln inner structure increases the capability of control over the material flow characteristics. Hence the overall quality of the product is increased due to improved heat transfer and flow control. Sustaining the level of quality becomes easier and safer. Manufacturing cost is decreased at the same time.
One of the key facts determining the product quality is the combustion chamber and automation. Design of the combustion chambers belongs to CMS and are compatible with gas fuels only. Rational burners are designed and manufactured by our suppliers due to specific requirements of the process. Burner and its automation unit is supplied within a single package.
Plant layouts and components change diversely due to specific requirements. Basic designs consist of following components;
- Crushing Unit: Raw stone is crushed in two steps and then screened. Final particle size is <~5mm.
- Feeding Unit: Crushed raw material is filled into stock silos with various volumetric capacities. The material is fed into the system under the control of feeding automation.
- Calcination Unit: The material is fed into the kiln via electronic scale feeder. During the calcination process, the material is transported through lifters inside the kiln. By the help of de-dusting system serially connected to the kiln, fine particles are collected. De-dusting system discharges the water vapour released as well. Filter bags of the kiln jet pulse filter are resistant to high temperature. Additional automatic fresh air dampers are placed for sudden temperature rises in order to protect the bags.
- Grinding Unit: The kiln discharge passes through the centrifugal mill (AD series). The particle size at the mill exit is <~700µm. The mill is designed only for grinding calcined gypsum. The grinded material is directed to cornice plaster filling unit or dynamic air classifying unit.
- Dynamic Air Classifying Unit: Air classifying process takes place after grinding. The material is classified by the help of an air classifier (SP series) into two semi products; satin finish and hand plaster gypsum.
- Stock Unit: The material is filled into adequate number of silos with the determined volumetric capacities. Calcite stock and big-bag feeding units can be placed on the sides of the stock silos or alternatively calcite can be transported via pressurized air.
- Satin and Hand Plaster Mixing Units: The material is weighed by electronic weigh batch hoppers before the mixing process. The batch is mixed by a powder mixer (TKC series) automatically. In every single batch, the weighing and mixing process is done simultaneously. After the mixture is ready, the material is discharged into the packing hopper for sack filling.
- Filling Station: Modular sack fillers (PMM and PME series) fill the bags within the range of 15-50kg. De-dusting of the filling station is done by jet pulse filters. Powder discharge during the filling process is recycled to the system.
- Calcite Raw Material Preparation Plant: Complete raw material preparation plant including all components. The material can be transported via big-bags or pressurized air.
- Automation management is done via central processing computer with SCADA. Process flow can be managed by using a mimic diagram. Simultaneous changes can be made, reports can be obtained, manual controls can be applied. Remote connections are available via ethernet module.
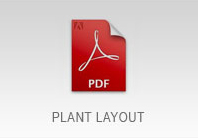
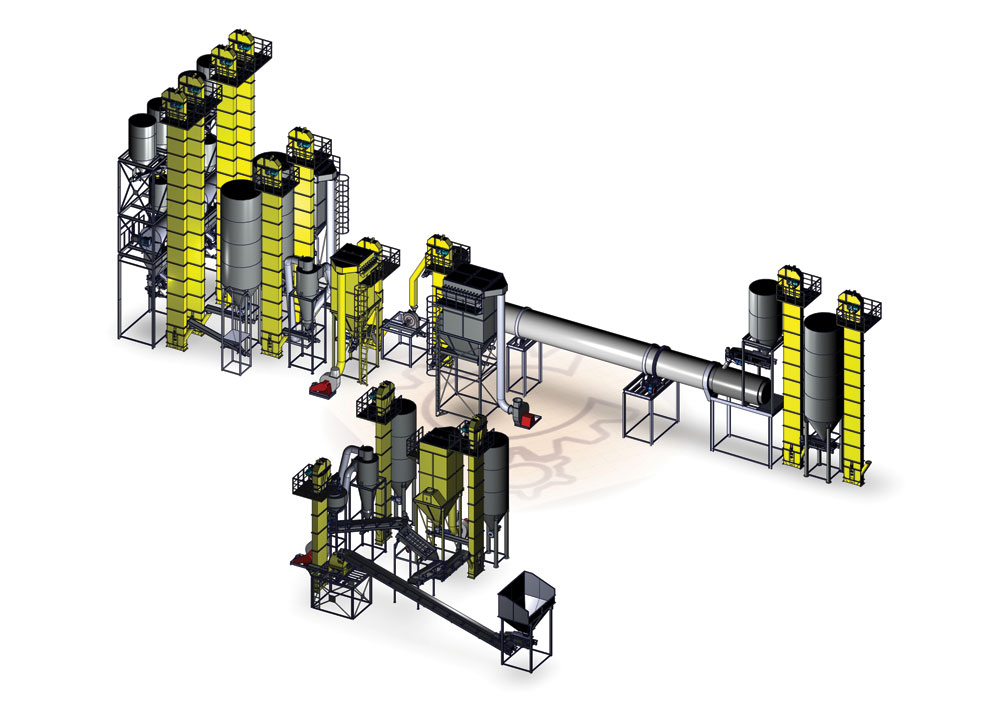
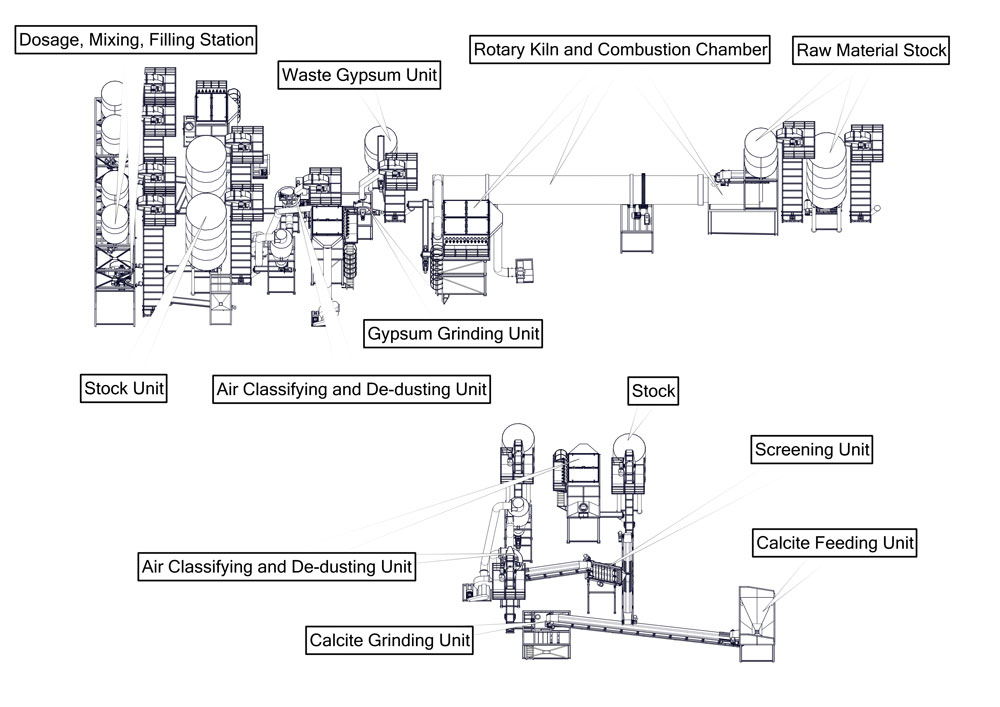