Products / Turnkey Powder Mixing Plants
Our company has over 30 years of experience on powder mixing plants. Turnkey powder mixing plants as a dry mix mortar plant for construction chemicals industry and as a subcomponent for powder gypsum plants and grinding plants are designed and manufactured in various capacities and layouts. Many turnkey installations are placed in Turkey and in the world.
Weigh batch hoppers are weighed electronically with a sensitivity of wt0,1%. Weighing and mixing process are done simultaneously. In order to prevent any errors in weighing, the mixing process is designed to operate with minimum level of vibration. This fact increases the overall sensitivity of the weighing process.
Our powder mixers are designed for sustaining minimum level of vibration with a fast, homogeneous mixing process. Parts and surfaces subjected to wear are lined with long lasting wear resistant steel plates. Hence the unit manufacturing costs are minimized for the process.
Sack fillers (PMM and PME series) are integrated at the bottom of the system. Easy operation and maintenance of these modular units makes filling process reliable.
Plant layouts and components change diversely due to specific requirements. Basic designs consist of following components;
- Calcite Raw Material Preparation Plant: Complete raw material preparation plant including all subcomponents in case of using calcite as a filler. The material can be transported via bucket elevators or pressurized air.
- Feeding Unit: Crushed raw material is filled into stock silos with various volumetric capacities. The material is fed into the system by screw conveyors under the control of feeding automation. Automatic pneumatic cutters are used for sensitive weighing.
-Weigh Batch Hopper and Mixing Unit: The material is weighed by electronic weigh batch hoppers before the mixing process. The batch is mixed by a powder mixer (TKC series) automatically. Mixing process is fast and homogeneous with minimum level of vibration. In every single batch, the weighing and mixing process is done simultaneously. After the mixture is ready, the material is discharged into the packing hopper for sack filling.
- Filling Station: Modular sack fillers (PMM and PME series) fill the bags within the range of 15-50kg. De-dusting of the filling station is done by jet pulse filters. Powder discharge during the filling process is recycled to the system.
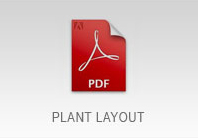
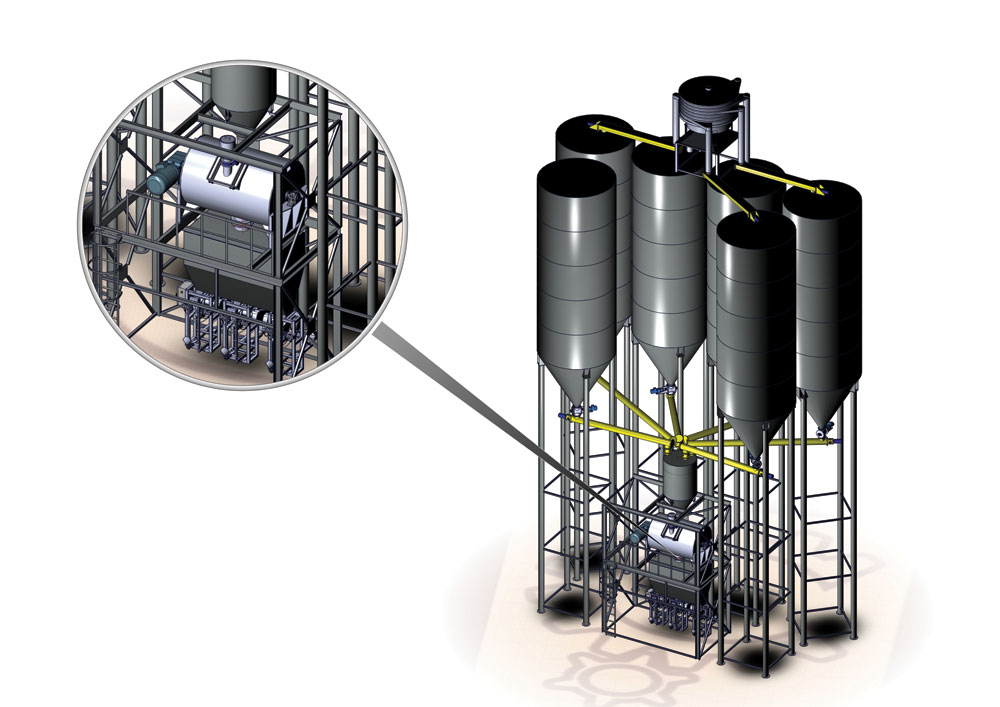
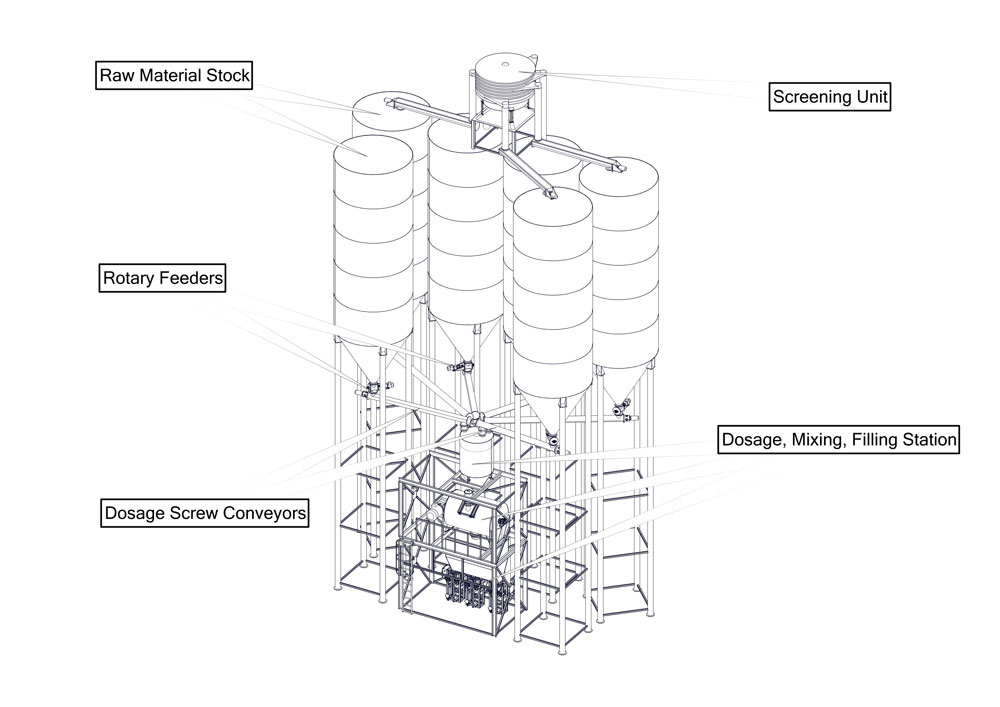